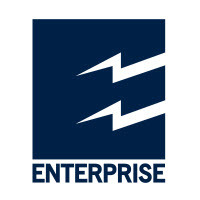
Description
Enterprise Products Partners L.P. is one of the largest publicly traded partnerships and a leading North American provider of midstream energy services to producers and consumers of natural gas, NGLs, crude oil, refined products and petrochemicals. Our services include: natural gas gathering, treating, processing, transportation and storage; NGL transportation, fractionation, storage and import and export terminals; crude oil gathering, transportation, storage and terminals; petrochemical and refined products transportation, storage and terminals; and a marine transportation business that operates primarily on the United States inland and Intracoastal Waterway systems. The partnership's assets include approximately 50,000 miles of pipelines; 260 million barrels of storage capacity for NGLs, crude oil, refined products and petrochemicals; and 14 billion cubic feet of natural gas storage capacity.
The Reliability Programs Senior Manager responsibilities include, but are not limited to:
Operational Availability
· Improve asset availability by exploiting company-wide data to identify common causes for lost availability. Develop strategies and solutions to reduce asset down time. Develop companywide processes to sustain consistent focus on asset availability.
o Define, collect, and leverage data from many sources to reveal insights into common or recurring root causes of asset down time.
§ Availability data
· Define and characterize unplanned causes of asset down time
· Collaborate with Operations Analytics team to develop consistent and efficient data structures to allow aggregation of availability information across assets
§ Computerized maintenance management system (CMMS) failure data
· Help define missing elements of failure data necessary to deliver complete failure analysis
· Propose procedural changes to ensure failure data collection is robust and sustainable
· Collaborate with and provide feedback to Enterprise's Maintenance Optimization Process team.
§ Operating data
· Operations daily reports and logs
· Findings and alerts from real-time advanced asset monitoring systems
Cross-Organization Improvements
· Identify improvement areas and champion recommendations.
· Oversee execution of improvement actions – while execution may fall under the responsibility of other teams, this role will report on status and have accountability for tracking and ensuring completion.
o Determine which issues can be assigned to existing teams for follow up and resolution, versus which require a new team to deliver sustained focus and management.
o Define new team functional and skill requirements, staffing, roles and responsibilities and job descriptions as necessary
o Ensure cross-functional coordination.
§ Collaborate with and serve as a hinge between other stakeholders, e.g., Operations Analytics, Operations, Reliability, Process Engineering, Controls Engineering, Commercial, Asset Optimization.
· Develop metrics to measure effectiveness and provide feedback on performance. Report on progress.
Asset Performance Management
· Serve as Enterprise's lead in the development and implementation of an asset performance management initiative with external business consultants.
· Investigate highly reliable processes and companies to identify best practices for achieving high availability.
Rotating Equipment Repair Oversight and Quality Assurance
· Develop a new repair shop inspection team to provide Enterprise oversight as critical rotating equipment repairs are conducted by offsite repair companies.
· Shop inspection team duties include:
o Support key rotating equipment shop work for all operating regions.
o Provide oversight and verifications of shop repair work quality
o Leverage knowledge of shop repair loads, quality of repair work, and shop staffing to recommend shops to use for rotating equipment repairs
o Cultivate third-party shop inspection contractors & contingent workers to meet demand & geographic needs
· Improve quality and success of rotating equipment repairs by:
o Providing independent oversight of shop effectiveness and quality
o Staying abreast of the dynamic repair market and understanding which shops are available and capable
Requirements
The successful candidate will meet the following qualification:
· Bachelor of Science in Mechanical Engineering is preferred, but other engineering degrees may be acceptable with relevant experience.
· 10 years of experience in hydrocarbon processing industries, particularly in the midstream, downstream, or petrochemical sectors.
· Organizational Knowledge – Understands Enterprise's organization and key contacts for gathering information and building consensus.
· Vision – Sets forth a vision of the future state, building upon but unencumbered by legacy processes.
· Current State Awareness – Understands the current operating environment, systems, data, and stakeholders.
· Focus – Maintains focus on key strategic program objectives; avoids diluting energy on current-day activities.
· Planner – Breaks down strategic goals into targeted tasks to create and execute a structured program.
Apply on company website